It’s Time to Get Circular in Our Manufacturing Processes
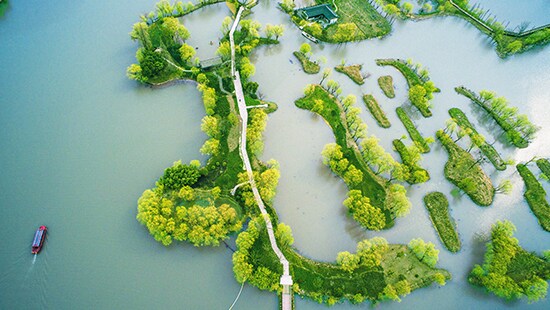
Sustainability is something that’s top-of-mind for businesses right now – and that’s good news. Sustainability is core to our purpose at Ecolab, and that includes the work we do around environmental stewardship. But what does that really mean?
At Ecolab, our approach to stewardship means managing and protecting resources that need to be cared for and preserved, including water. Bottom line: it means we help our customers grow their businesses profitably while doing right by the environment.
We truly ‘walk the talk’ by making sure we’re managing and protecting resources within our own operations – and our global supply chain plays a key role. But we face a challenge between balancing long-term goals with the day-to-day work and realities within our facilities.
One way we’ve been able to drive progress in the last few years is as a founding partner and member in the Alliance for Water Stewardship (AWS).
In 2014, during the height of a drought, our Taicang, China, plant became the first facility in the world to be certified under the AWS Standard, which helps facilities make decisions and take action to use freshwater sustainably. Since that time, we’ve implemented the standard at two facilities in California with plans to achieve certification for our Garyville, Louisiana, plant by the end of this year. We’ll continue to focus on achieving certification for additional facilities in the coming years.
What’s next? Taking a circular approach in our manufacturing operations
As we evolve our water stewardship journey, circular water allows us to manage this critical resource more sustainably in our operations. While most water strategies are linear – thinking of water in terms of intake, use and discharge – a circular approach looks at the context in which our facilities operate, and builds a water management strategy that takes into account the location, quality, quantity and the value of water relative to your organisation’s processes and long-term success.
So, what would a circular approach look like at Ecolab?
Reducing water use annually by up to 20% - Clearing, Illinois
Our plant in Clearing, Illinois, is Ecolab’s largest producer of colloidal silica, which is in everything from nanotechnology to LED lights to smartphone screens. But manufacturing it takes a lot of water.
By reusing process water, we’ve been able to expand manufacturing while using less water per ton. And we installed a water reclamation system, which will reduce the plant’s water use by up to 20%.
This facility proves that older plants can be just as smart about how we use water as new ones. Customers will be able to learn about these projects and technologies at our Clearing Customer Experience Centre, which opens to the public this September.
Reducing water intake by 85,000 gallons a day - Garyville, Louisiana
Located in Garyville, Louisiana, our second-largest manufacturing facility uses water from the Mississippi River in its manufacturing process.
River water needs to be pre-treated before its used in the manufacturing process. By reusing water to effectively treat the river water, we were also able to reduce the plant’s intake of river water by 85,000 gallons each day. By running the pumps less often, we were able to use less chemistry and save electricity as well.
This is just the beginning
These are just a few examples of the work we do every day to ensure we’re protecting and preserving resources in our own operations. To learn more about our sustainability efforts, I encourage you to check out our latest corporate sustainability report, available at Ecolab.com/CSR.